Pressure instrumentation is found in almost every process plant. Verifying the calibration of these instruments is a necessary part of ensuring these instruments deliver accurate measurements to the control system.
Calibrating these instruments correctly where installed can often be frustrating, but, it’s a necessary part of optimizing process operations and ensuring plant safety.
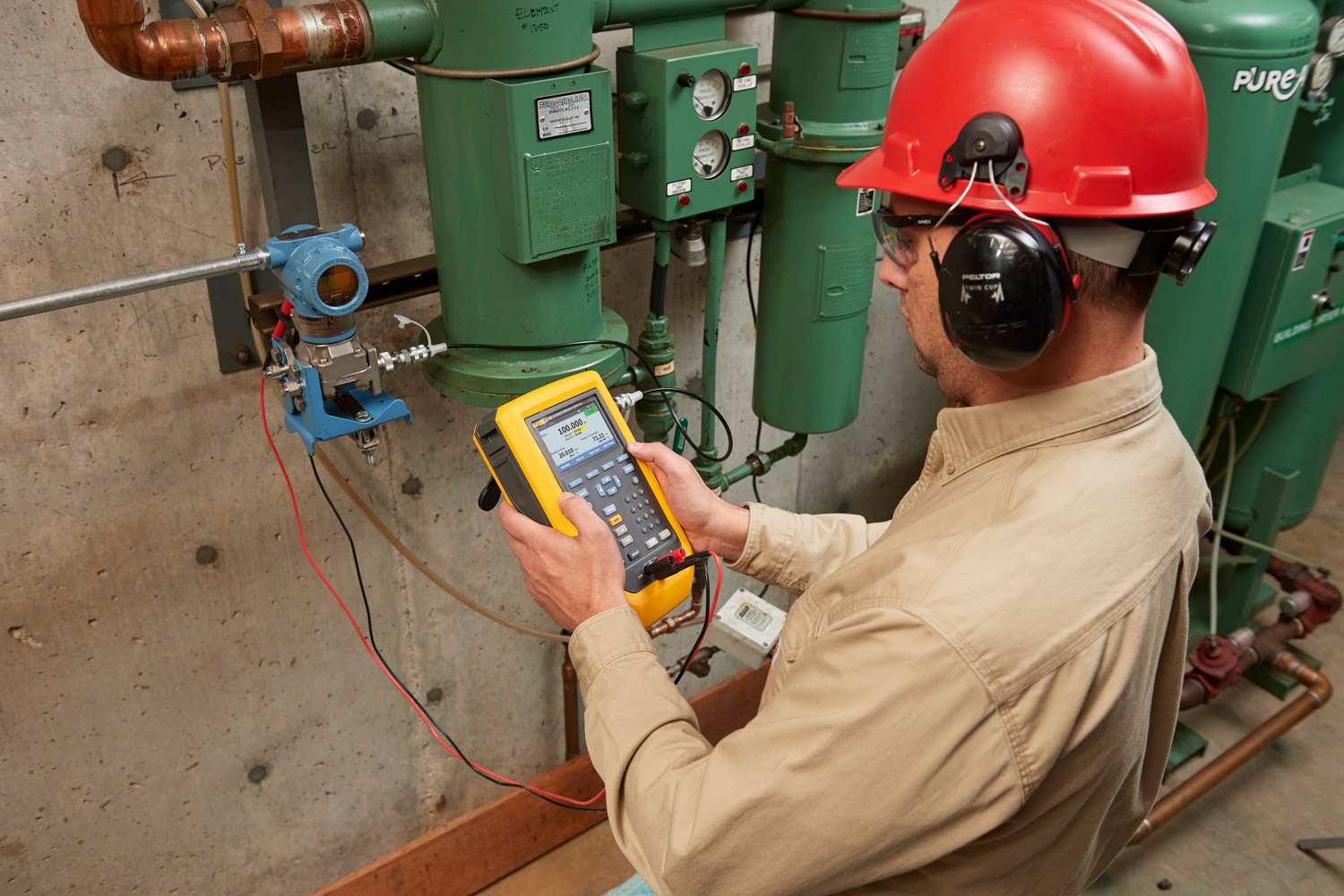
In many businesses, the measurements taken are how prices are established. Business hinges on everyone involved getting accurate and fair numbers. Regularly calibrated pressure and temperature transmitters is the best way to ensure accurate measurements with a high degree of certainty. Taking the extra step to calibrate helps to guard against any incorrect measurements and double checks the flow throughout process control systems.
Performing a pressure calibration with a slow leak
To properly conduct a pressure calibration, you need dependable equipment and pressure connections. If you’re dealing with a leaking pressure source, it can make it hard to keep the pressure stable at a calibration point long enough to get a reliable reading.
A slow leak may require constant fine tuning and pressure adjustments applied from a pump, which makes it difficult for the system to settle so get the reliable readings you need. It’s recommended that you let the system settle for several seconds up to a minute, after you reach the pressure set point and before you record or document your calibration tests. This creates a more accurate and repeatable test result.
While slow pressure leaks caused by damaged hoses, worn fittings, or improper connections are common, follow these steps to get more accurate calibration results.
- Test and debug the pressure test systems before entering the field to reduce additional trips back to the shop.
- Limit the number of pressure connections, when possible.
Use the correct length of hose instead of splicing smaller pieces together. Remove extra fittings throughout the system wherever you can. This gives you fewer weak points for leaks to easily occur. - Double and triple check that the test equipment is properly connected.
- Use special-purpose test hoses and fittings to mitigate leaks you may come across.
There are test hoses designed with “no tools required connections” to make these connections easier. - Use a pressure calibrator with an internal, automatic electric pump.
The Fluke 729 Automatic Pressure Calibrator has an internal, automatic electric pump. It can self-regulate pressure during tests, so you don’t have to make manual adjustments as you run a test. The automatic pressure regulation compensates for slow leaks in test setups so you can get more accurate, dependable results.
Simplify the pressure calibration process
Manually generate and control pressure for each test point
In process manufacturing facilities, you need to use a test strategy for multiple test points; anywhere from three to eleven different test points, the most common being a 5-point up and down test. Trying to adjust and fine tune the system pressure for each of those specific points can be both time consuming and difficult. Each individual point requires you to increase or decrease the pressure; pump the system up or release pressure, and then fine tune the pressure using a vernier, or fine adjustment mechanism, on the test pump before you can get back to work. Instead of spending the time here, just get the right pressure calibrator.
With the right pressure calibrator, you can easily generate and control the pressure for each test point. You can simplify the process by inputting the upper and lower range values of the test along with the desired strategy of set points and let the calibrator run through the process on its own. Without hand pumps or manual adjustments.
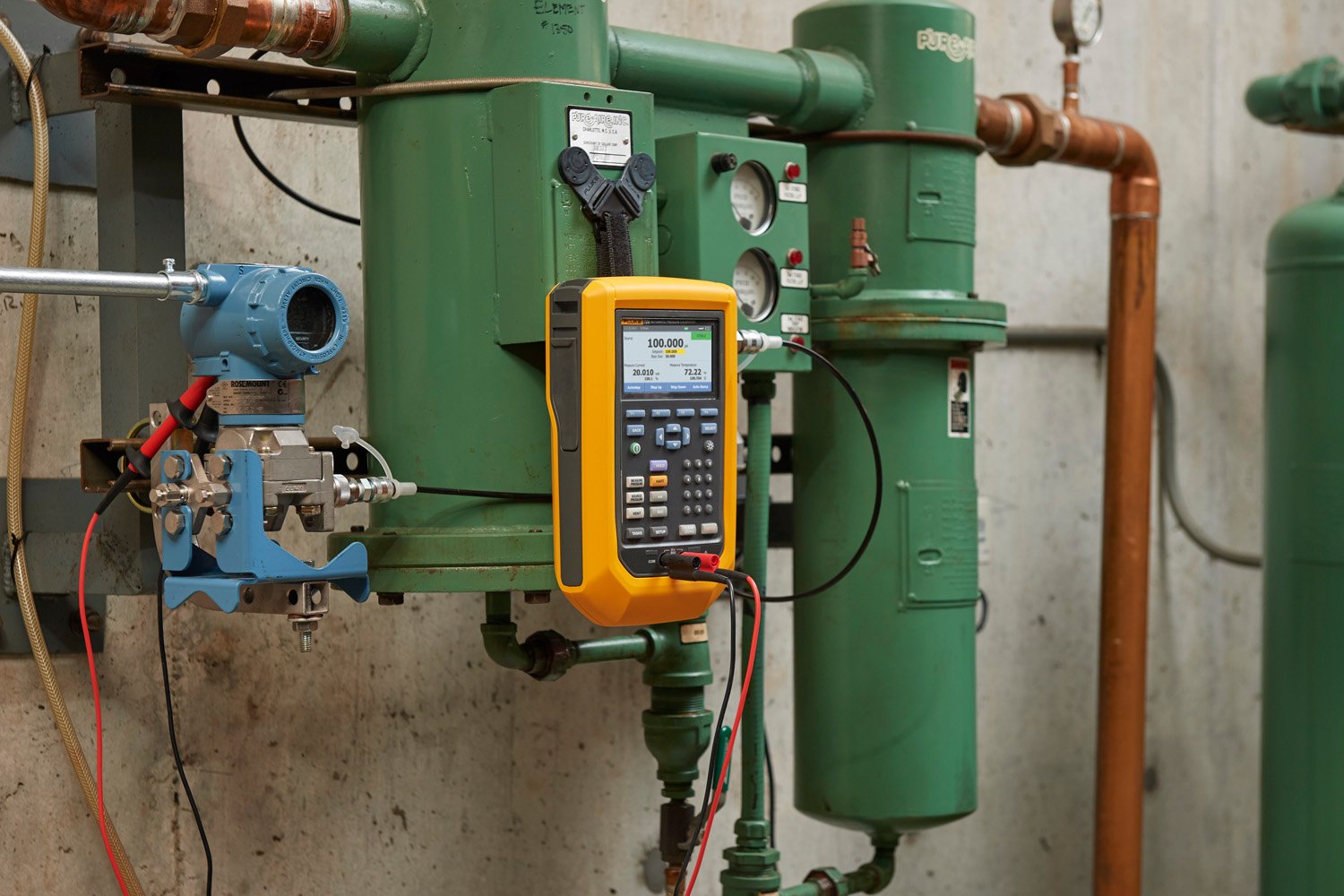
Repeatability is key when calibrating a pressure switch
When it comes to calibrating a pressure switch, repeatability is the key to success, especially since it can be a time-consuming process. The steps you want to take to achieve repeatability require you to apply slow pressure changes as the switch approaches its defined set or reset points. This process requires determining where the switch sets, and you need to make sure the vernier on your test pump has the capability of varying pressure up to the set point and back to the switch reset point. Making these adjustments manually is a process that’s difficult to repeat.
Sure, you can get the fine adjustment of the pump within range of the set and reset point pressure more regularly with practice, or you can simplify the process further.
Select a pump with a wide adjustment range so you can more accurately make adjustments that meet the UUT measurement needs. Or, select a 729 Automatic Process Calibrator that will automatically find and document the switch setpoint, reset point, and deadband. Creating the most repeatable and time-saving option available.
Documenting a field pressure calibration
The last piece in the process is documenting what you’ve done. You want to maintain accurate critical measurement records and allow for traceability back up the calibration chain. This is another complicated step that can easily be simplified with the right tools.
It’s hard to juggle the documenting manually while pumping manually and writing down the test results. The calibration tools need to accurate enough and cover the correct measurement range for the test. Often if on a calibration route you need to plan for multiple calibrations.
Plan ahead before leaving the shop and be sure to have the specific test procedures or method sheets you need for each pressure device you need to calibrate. Alternately, a Fluke 729 Automatic Process Calibrator can do the documenting for you, and cut down on the number of different tools you need to bring along with you, clipboard, paper, and pen not required.
Automated documentation makes managing calibration data incredibly easy for you. The calibrator can automatically document the results as you’re running a test. The 729 will then flag out-of-tolerance test results in red on the graphical display for:
- Applied pressure
- Measured mA,
- Measured mV
- Measured digital PV
- % error for each test point you set
With Fluke Connect® compatibility, the 729 also lets you perform remote where you can manage and store pressure measurements and logging events.