Energy conservation programs don't have to entail major investments in new equipment and systems. Often facilities maintenance teams and/or outside contractors can achieve significant savings in electric power used and billed just by testing and tuning up the systems they have today. With just operational changes or different maintenance practices, they can find savings to strengthen the bottom line, reinvest for even greater savings, or both.
The skilled labor and test tools used for such an audit don't come free, but their cost can be minimal when measured against the possible savings. The table below provides an overview of what systems to test, which tools to use, how to test and how to mitigate problems you find in major electrical distribution and motor-powered plant systems. Contractors or facility maintenance teams can use this process to show facility leadership savings that are simple to execute, and promote an incremental approach: start small, offer savings all the way through, and add new steps as they secure savings.
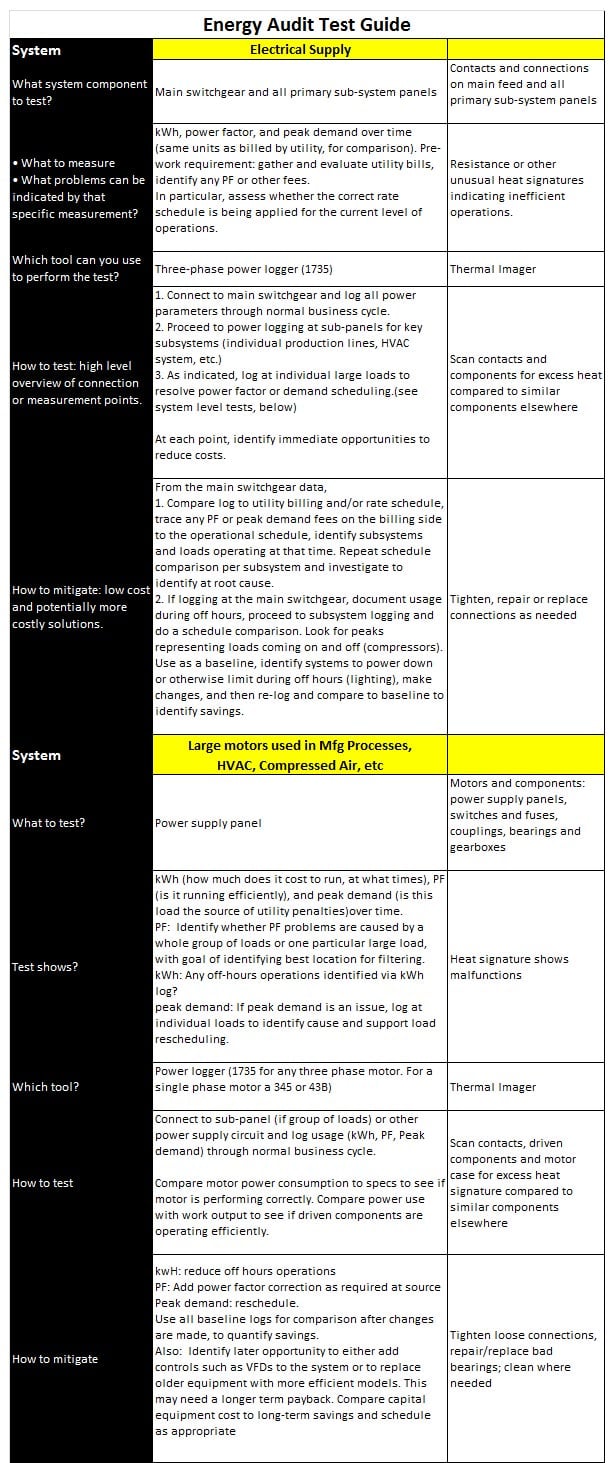
Tool list:
- Fluke 289 True-RMS Data Logging Multimeter
- Fluke TiS55+ Thermal Camera
- Fluke 1735 Power Logger
- Fluke 345 Power Quality Clamp Meter - Electronic Power Meter
- Fluke 417D Laser Distance Meter
- Fluke i400s AC Current Clamp Accessory